Max-Line Connected developed to reduce maintenance costs
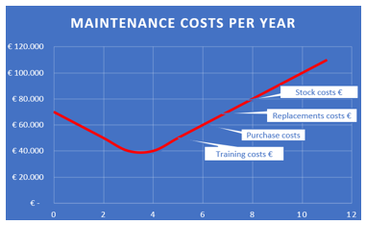
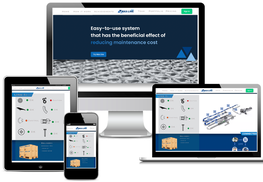
Max-Line Connected
Max-Line Connected is a clear and user-friendly system that has a beneficial effect on maintenance costs. It shortens the procedure of replacing a spare part, thus achieving optimal standardization.
How does it work?
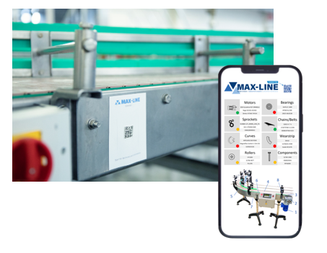
Max-Line Connected
Max-Line connected is the only system on the market that combines all systems. By scanning one QR code attached to the transport conveyor the following data becomes available:
- Conveyor motor
- Drive bearing
- Idler bearing
- Chain/Belt
- Drive sprocket
- Idler sprocket
- Curve
- Wearstrip
- Rollers
- Roller conveyors
- Customer code
- Stock location code
- Maintenance history
- Spare parts status
- Quantity of parts per conveyor
- Total overview parts
- SAP migration

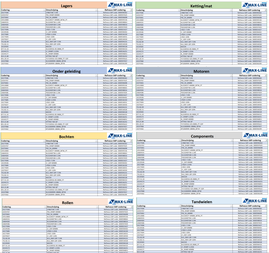
Optimal Standardization
The factory clearly sees the number of spare parts per production line. Optimal standardization can be achieved, thus reducing expensive stocks. Standardization clarifies which spare parts we can permanently remove from the stockpile. Inspect-Scan-Purchase-Replace.
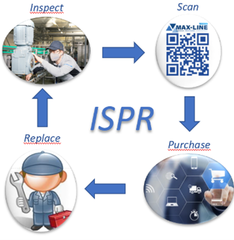
Inspect-Scan-Purchase-Replace.
After scanning the QR code, an internal technician immediately has access to the stock and SAP customer codes. It allows them to order the spare parts directly or to locate them in the stockpile. We call this ISPR. The most efficient way from inspection to overhaul.
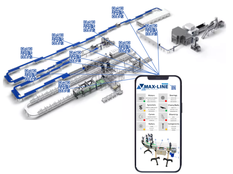
Max-Line Connected Offers a Unique Maintenance History per Conveyor
Max-Line connected offers a unique maintenance history per conveyor. The maintenance technician in charge receives a Max-Line connected account. It allows them to scan the conveyor with their phone and perform the following actions:
- Status Change of Spare Parts
- Inform the work preparation on spare parts type
- Look up the stock location of spare parts
- Make a note of the work in the maintenance history
- Set transport conveyor to status 'inspected'
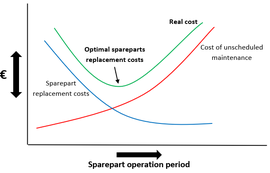
Analyzing a Balanced Annual Budget
Based on the annual budget resulting from the annual inspection, it is possible to estimate which spare parts need to be replaced to prevent malfunctions. We can significantly reduce maintenance costs by replacing the part at the right time. Optimum replacement momentum.